Quality department
Ensure impeccable quality for your products
Meticulous inspection services to guarantee the excellence of your products
Your Products, Secure Throughout the Supply Chain
To ensure the excellence of your products, our team has put in place strict supplier qualification protocols based on 137 precise criteria.
The skills of our Quality Department are :
Inspections to guarantee product conformity
To guarantee the conformity of your products, we organise rigorous inspections throughout the supply chain, from initial production to final delivery.
Thanks to our experienced teams and precise protocols, we can identify and correct any discrepancies before they become a problem.
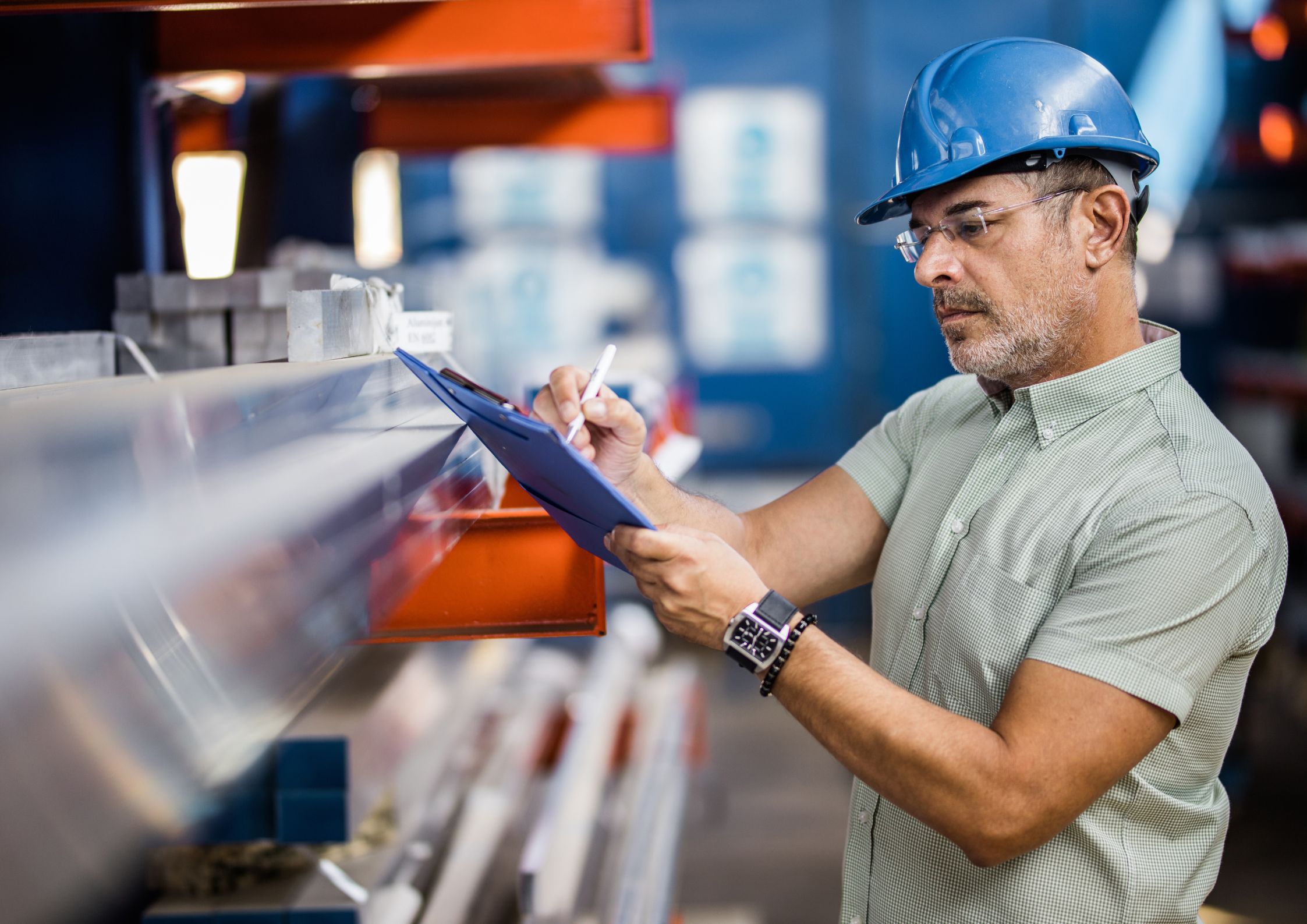
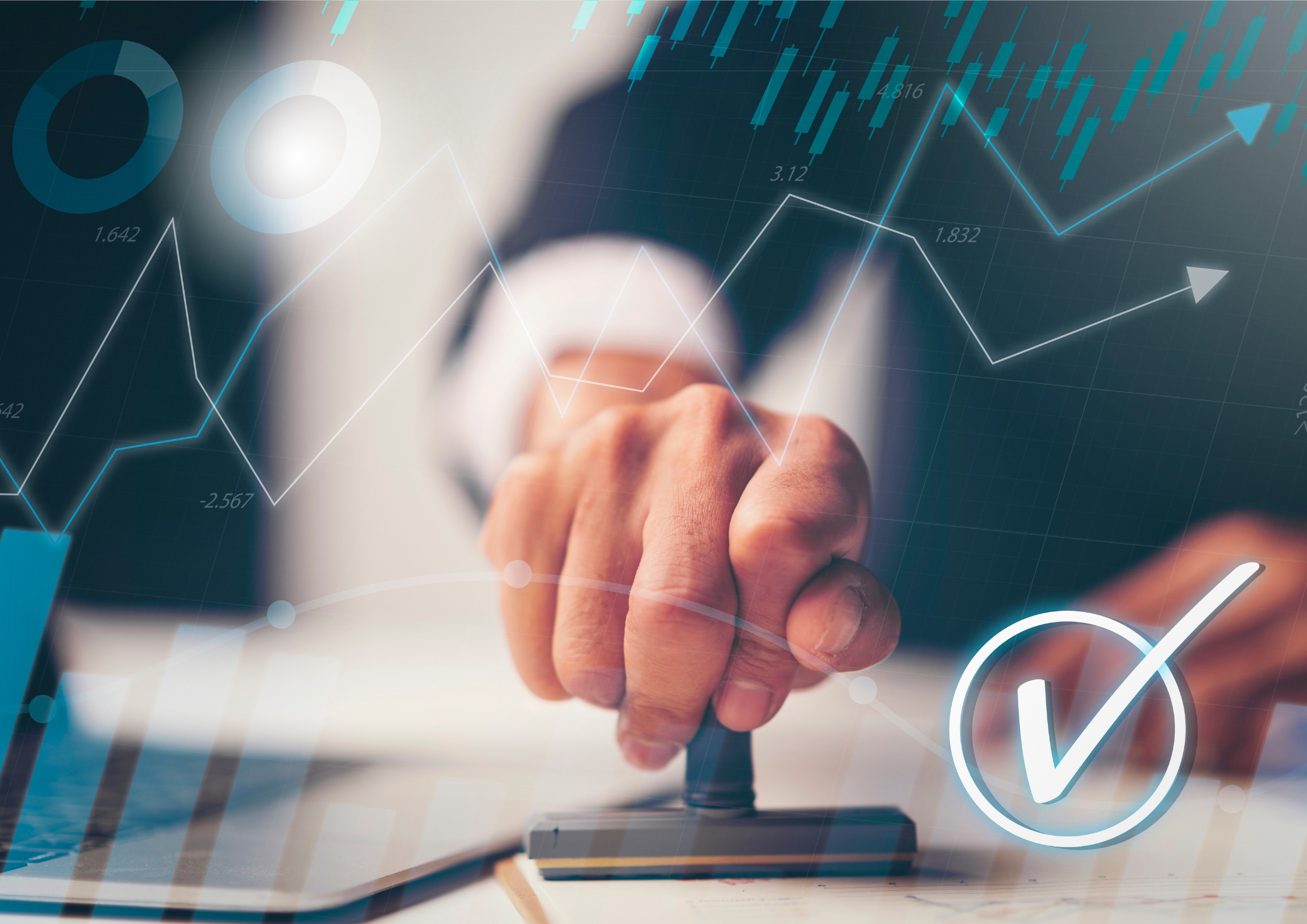
Tests and checks according to
International Standards
We carry out rigorous tests and in-depth checks to ensure that your products meet the following requirements
your requirements.
Working with certified laboratories and technical experts, we check every detail, from material composition to functional performance, to reduce the risk of non-compliance.
Our service Plant Audits
and Laboratory Tests
Your guarantee of Quality and Conformity.
Plant Quality Audit
& Partner Laboratories
We carry out in-depth audits of partner plants and laboratories, assessing their capabilities
quality control processes,
their certifications, and their compliance with international standards.
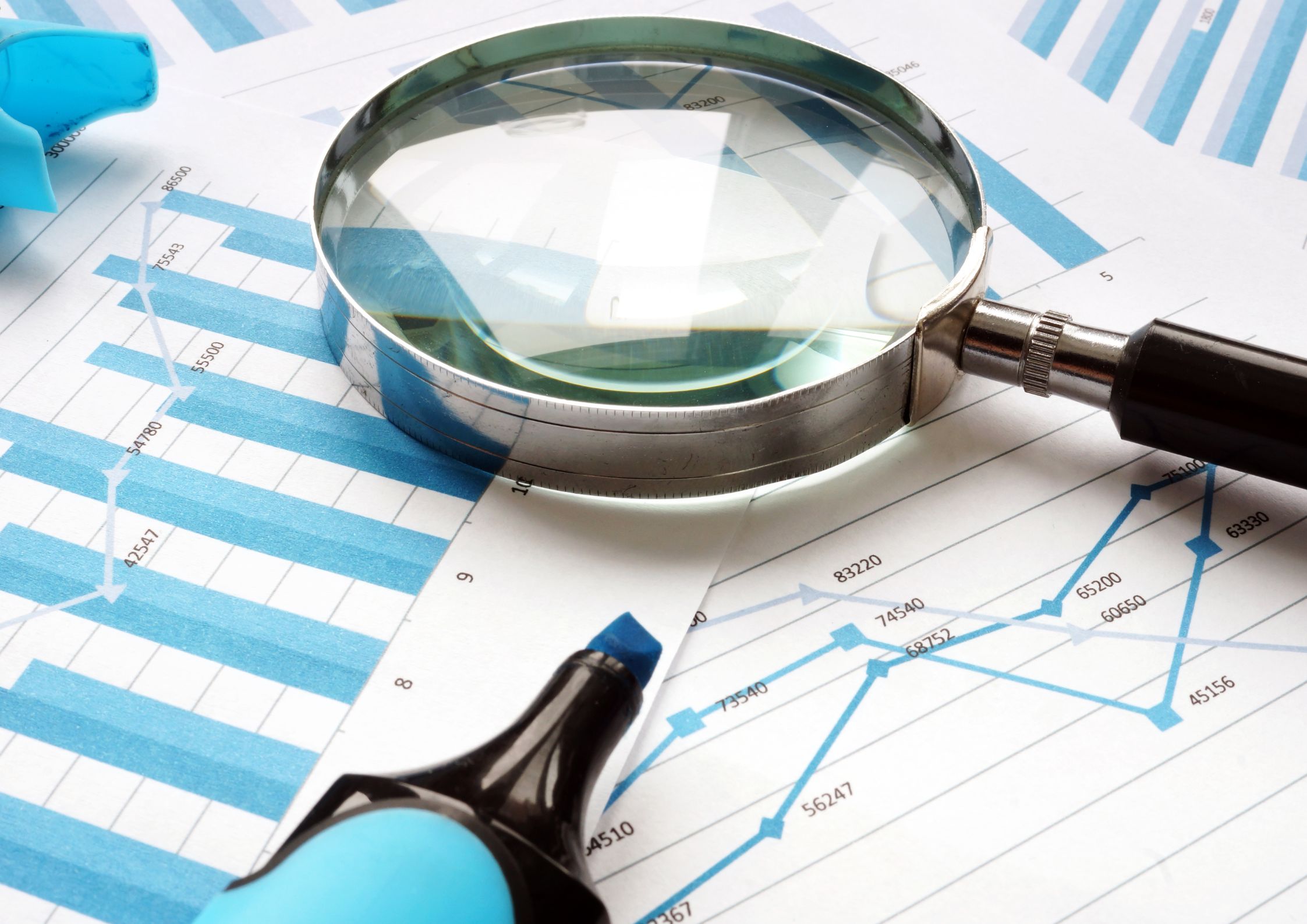
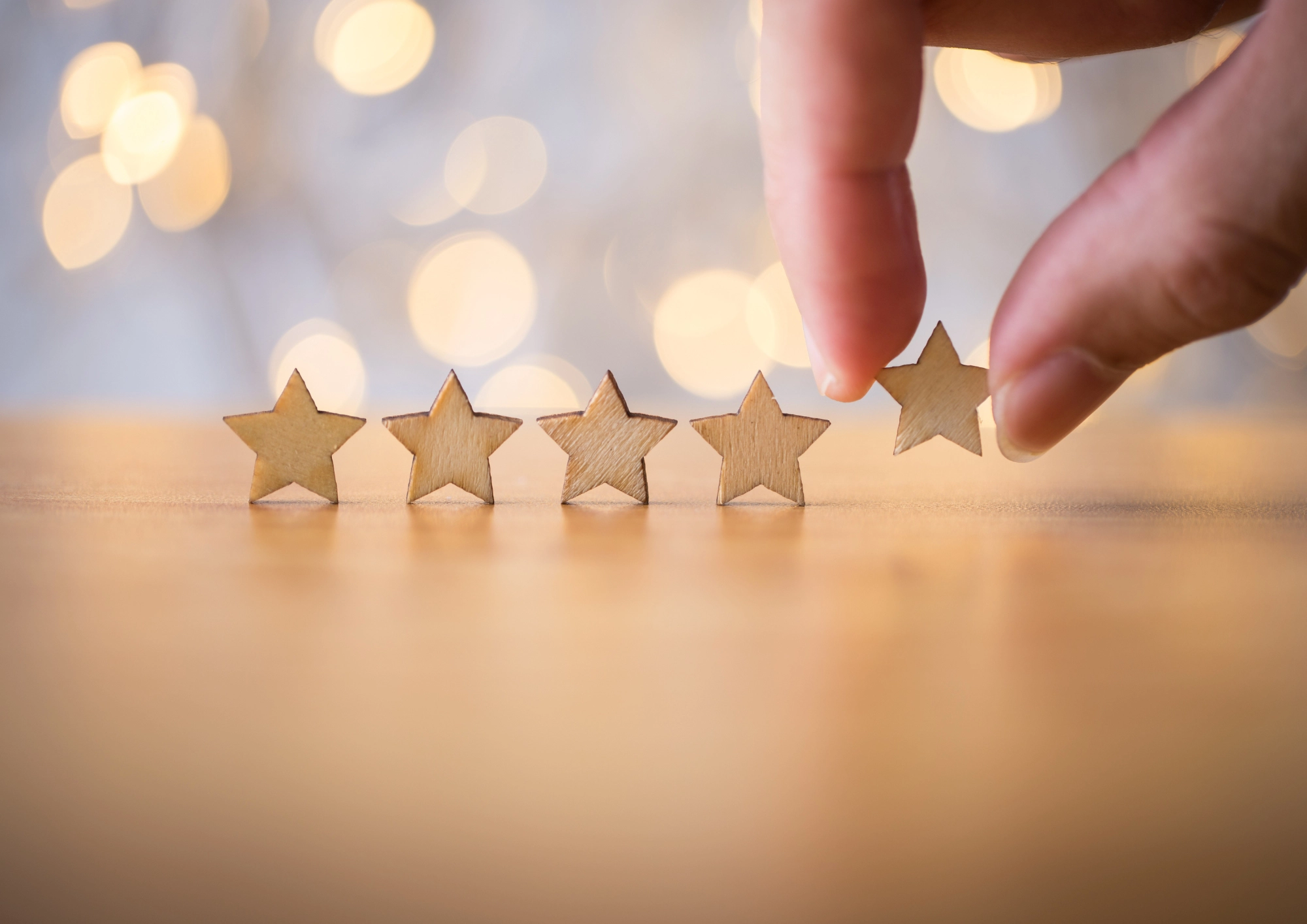
Certified Excellence
and Reinforced Controls
These audits enable us to identify our strengths, detect any shortcomings and recommend improvements.
By choosing validated and reliable partners, you minimise operational risks and ensure that your collaborations support your strategic objectives.
Ensure the quality of your products
at every stage of production
Each product is rigorously tested to ensure performance, reliability and safety.
Control processes
Strict quality
We put in place appropriate quality control processes
at every stage of production, from the selection of raw materials to final delivery.
Thanks to constant monitoring and a precise methodology, we detect and correct any anomalies in real time, ensuring that your finished products are beyond reproach and comply with the highest quality standards.
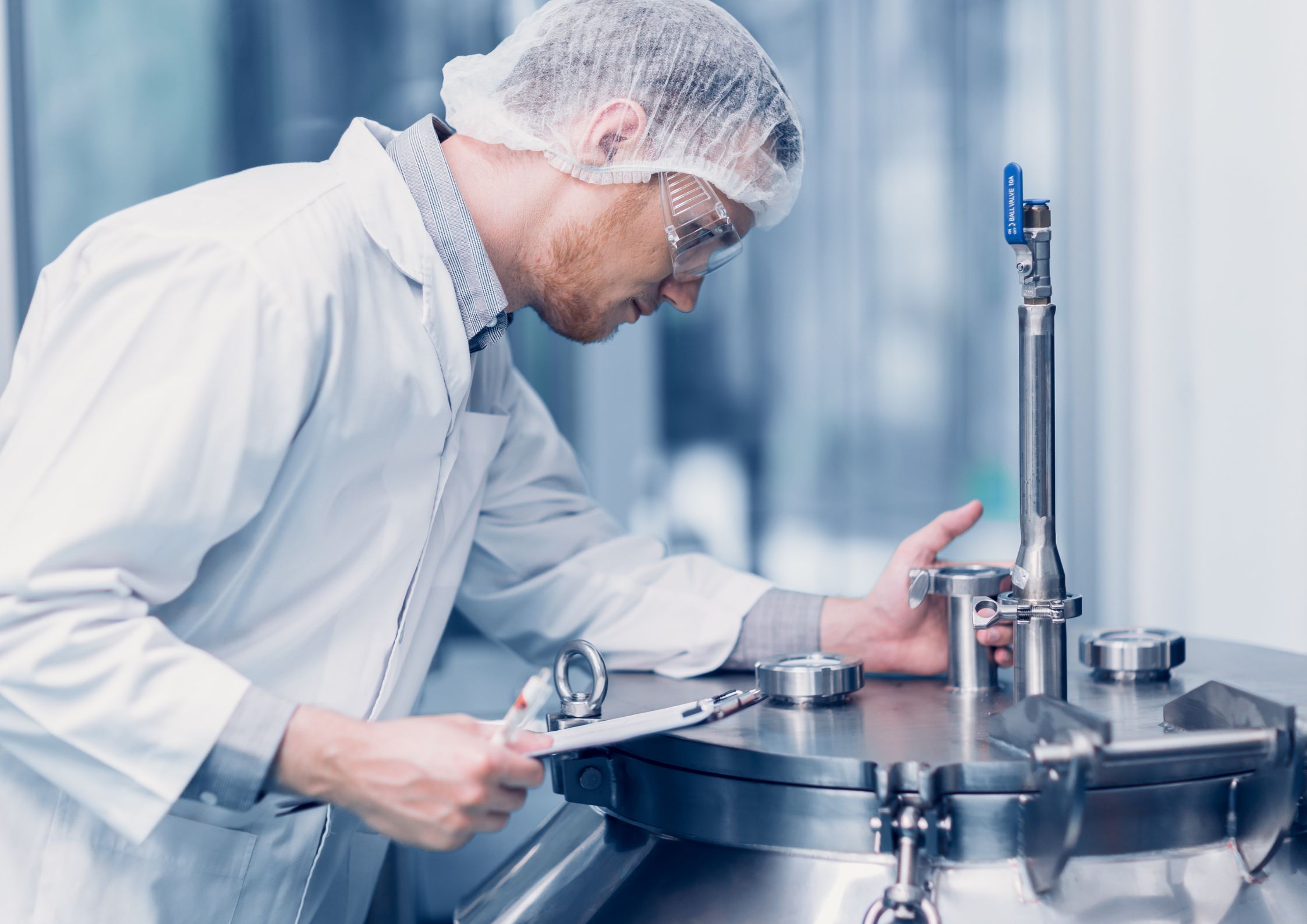
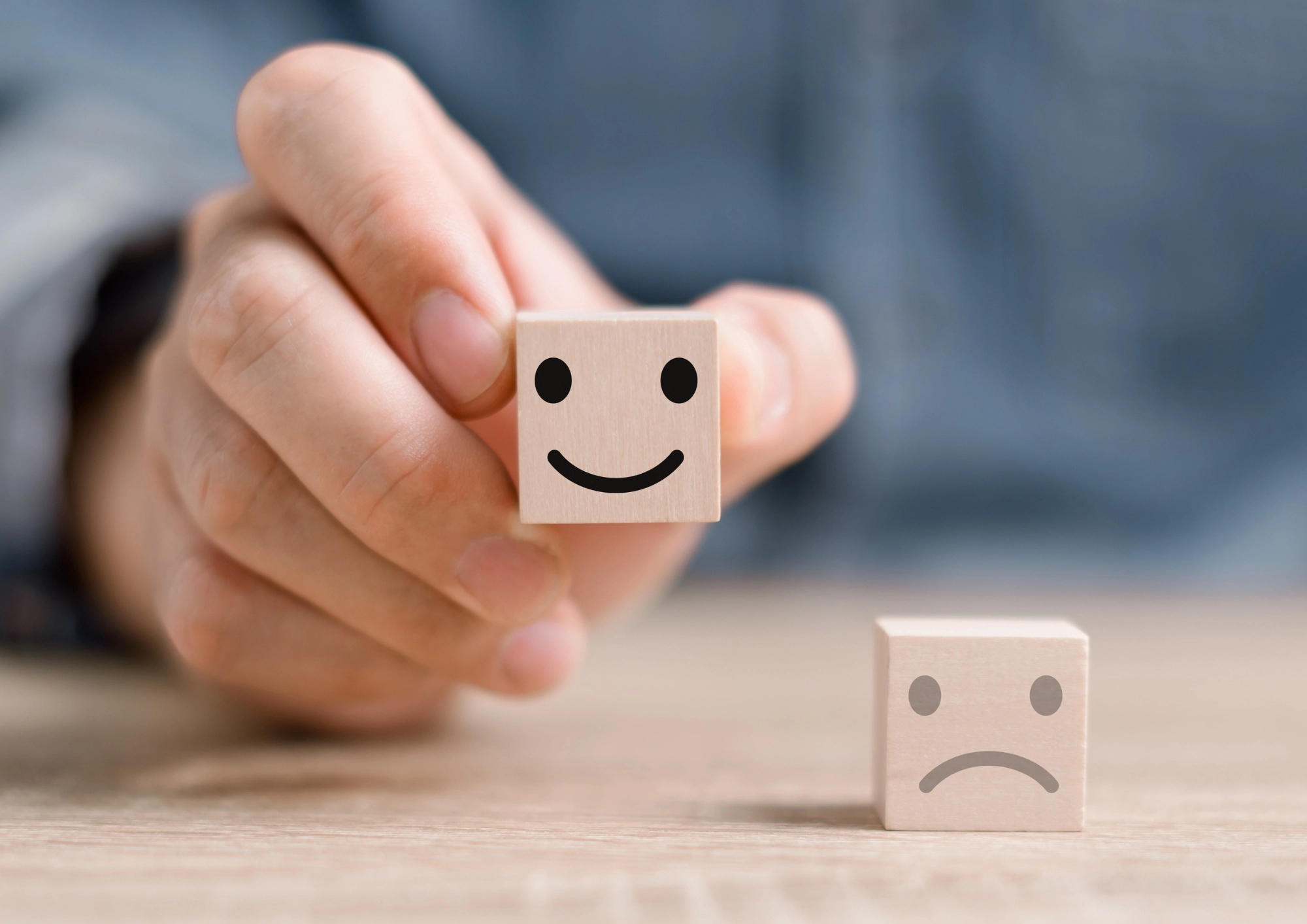
Complaints management
and Customer Returns
Every claim is handled carefully, with in-depth analysis to understand the cause and prevent future occurrences, and rapid problem resolution.
We also work to manage product returns, offering tailored solutions that meet your expectations while minimising the operational impact.
Our assets
A team inspectors in the field to evaluate factories directly and provide you with detailed reports
and transparent.
worldwide
Take advantage of our global network of partner laboratories for rigorous inspections, wherever your products are manufactured or shipped.
Specifications
Every customer has unique requirements, That's why we offer you maximum flexibility when drawing up your specifications.
Compliant
Our expertise and network of partners guarantee rigorous checks on every product, in compliance with directives and regulations.
par An
Everyday
per Month on Average
Frequently Asked Questions
Quality management is crucial to ensuring that products meet your standards and expectations, to minimising the risk of defects, and to maintaining your company's reputation in the global marketplace.
To ensure quality, it is important to carry out regular audits and inspections of suppliers, draw up clear and detailed specifications, produce samples and test products before dispatch.
Best practice includes checking suppliers' quality certifications, assessing their performance history, carrying out on-site audits and putting in place contracts with specific quality clauses.
In order to address quality issues, it is important to communicate quickly and clearly with the supplier, document the issues, collaborate on a corrective action plan and monitor progress to ensure that improvements are implemented.
A quality standard, such as ISO, establishes uniform criteria that suppliers must meet. It facilitates trade by ensuring that products meet globally recognised standards, thereby reducing the risk of non-compliance.